By Marcelo Hirschfeldt, Instructor y Consultor en áreas de Tecnologías de Producción y Gerenciamiento de Activos Petroleros
INTRODUCTION
ALS MANAGEMENT CONCEPTS. The comprehensive management cycle of Oil field development using ALS´s, involves different inherent processes and participants, which makes necessary an integral scheme of management. Identifying each of the stages and people who take part in the processes is fundamental to be able to optimize existing procedures or implement a comprehensive medium and long-term management strategy. The scheme in Figure illustrates a management cycle during ALS´s implementation and operation, and can serve as a guide to analyze different aspects of the whole process. Two stages are identified: initial evaluation, for initial selection and implementation; and the Integral Management ALS Cycle, which by its own development, it becomes in a positive feedback cycle (virtuous circle) where different work participation areas and interdisciplinary work becomes key factors for a correct management.
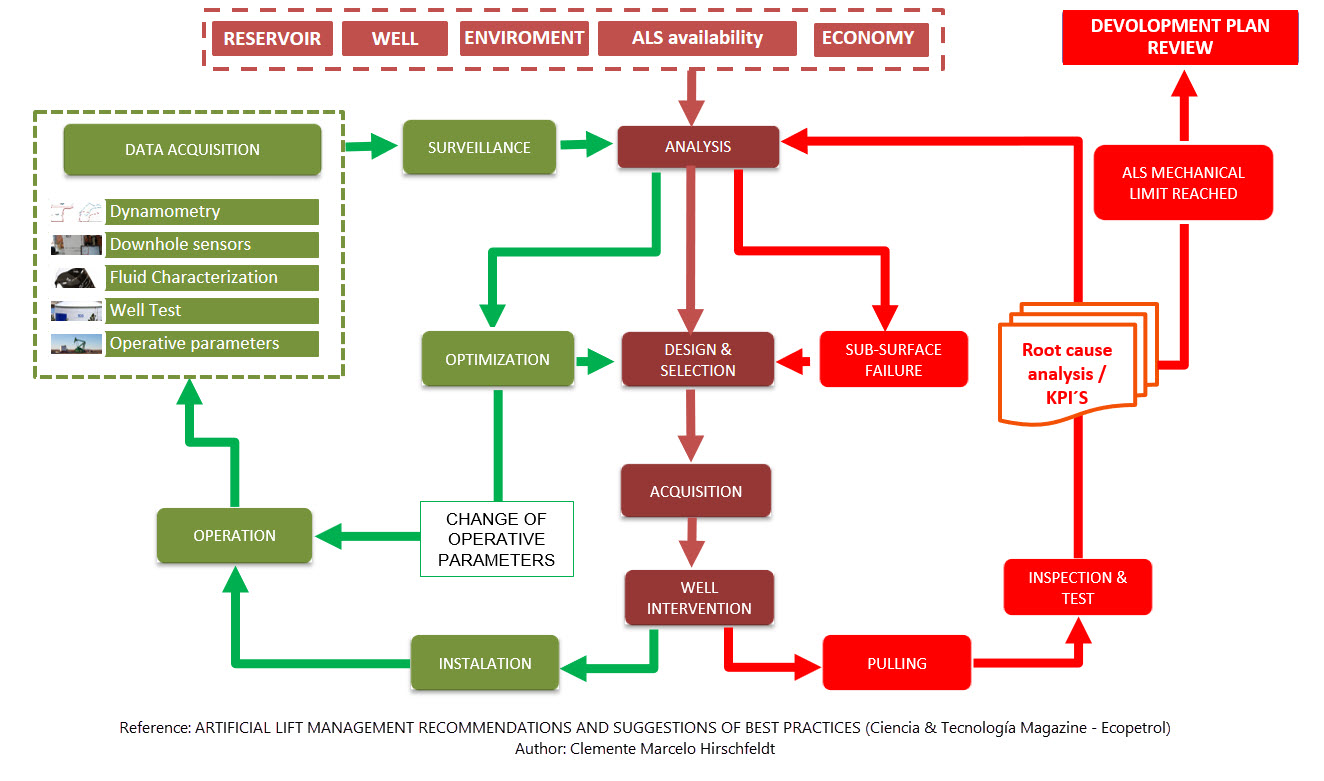
This cycle starts with one or more ALS´s alternatives selection based on the analysis of information on the reservoirs to be produced, well construction data, and other aspects that will be discussed throughout this article. Based on this analysis and once the best method(s) have been selected, equipment acquisition, installation, and operation are the next stages, which complete and closes one of the first sub-cycles in a comprehensive management system.
Once wells have been started up, monitoring and control operating variables are essential not only to guarantee optimum ALS operation within established parameters, but also to maximize reservoir production. Continuous analysis may point out the need to work on the system in operation, either based on surface actions like (changes in sub-systems or some operating condition), as well as down-hole actions; either by replacing elements, or the whole installation, or even the type of ALS in certain area, in order to meet development objectives.
Components failure on already installed and operating ALS´s is another situation that may happen, which corresponding analysis and evaluation thereof, should provide information for decision making in future ALS selection and/or design. In other cases, when ALS mechanical limit has been exceeded, oil field development strategy may have to be redefined considering topics like implementation of secondary recovery projects, rethink of geometry and well depth, etc.
The management cycle above explained,represents in summary the know-how in artificial lift management in Golfo San Jorge Basin (Argentina), where widespread use of ALS´s since the beginning of its operation is common. However, this work strategy could be considered for other kind of oil field operations.
SELECTION CRITERIA BASED ON MECHANICAL LIMITS
During the second stage of the hole process, design, operation and optimization sub-processes come into active play, several challenges are faced, many of them particularly present and or exacerbated in the case of unconventional fields. Complexity of many of the non-conventional oil deposits is not only present in terms of the characteristics petro physical of the reservoir and of the fluids contained, but also in the geometry (dogleg severity and azimuth) and completion characteristics (fracture hydraulic or other stimulation technics) of producing wells, which make these reservoirs and wells unconventional themselves. Some factors related to ALS mechanical limits for unconventional reservoirs, that should be considered are:
Dogleg severity and azimuth – Mainly in ALS´s using sucker rods (SRP and PCP), system reliability is based on minimizing wear between tubings and sucker rods, as well as sucker rods fatigue. In both cases the use of anti-wear mechanisms is essential. For ESP applications, Dog leg severity could affect to power cable integrity as well as to engine and seals. ALS´s Systems without sucker rods like HJP and GL could be evaluated as alternatives, their use should be analyzed depending on the expected time between failures.
Gas handling – Depending on natural and/or mechanical gas separation that can be done, this condition may limit the use or the volumetric efficiency of systems such as SRP and PCP. In the case of reciprocating pumping it may cause partial filling of the pump resulting since low efficiency to total lock (gas lock). On the other hand, with PCP systems, even when certain amount of gas is controllable (without locking), too much gas may cause poor lubrication between stator and rotor, and subsequent rupture, gas absorption by the elastomer or an heterogeneous pressure distribution along the pump stages can create pump failures or poor performance of the system. For ESP systems, gas separators, Advanced Gas Handler (AGH) and/or multiphasic pumps will be required, depending on the gas-oil relationship (GOR). Systems as gas lift and plunger lift (depending on the flowrate) are friendly to the handle and use of gas.
Compatibility with fluids produced – Mainly associated with PCP systems, where compatibility of the elastomer of the stator with fluids produced is essential to ensure the life of the system it. So, is imperative to predetermine presence of Aromatics, H2S, CO2, among other components, as well as implement elastomer compatibility testing with wellbore fluids before installing. If the fluid composition produced is unknown, less susceptible systems should be considered for the evaluation of wells.
Flexibility in flow rate produced – Whether during an abrupt production decline phase, such as in the case of low productivity compact deposits, or for increasing production areas under EOR processes, ALS systems flexibility to accommodate wide well production rates, without major modifications to the surface or subsurface installation, is essential.
Uncertainty in the productive potential –Uncertainty in the productive potential, coupled with a sharp production decline may result in an operational condition called “Pump-Off”, in which no more fluids from the reservoir enters to the pump. To prevent this condition, the operation with increasing flow rate and a strict fluid level monitoring should be realized. In the case of PCP systems, this condition is critical because the stator elastomer requires to be lubricated, and the use of downhole pressure and temperature and variable speed drive (VSD) sensor should be considered. In the case of ESP systems, if it shall be subject to very low fluid velocity to cool the engine and also by the lack of fluid, these situations will cause motor failure or stop of low current to the motor. Under these conditions, downhole pressure and temperature monitoring systems and variable speed drives (VSD), are valid alternatives to protect the equipment. If the productive potential is unknown, high capacity and more flexible systems should be considered for the evaluation of wells.
Well depth – Fluids production from wells is directly related to hydraulic horsepower concept (the higher pressure and flow to be pumped, the greater horsepower required). Systems that use sucker rods as PCP and SRP, will be limited to maximum mechanical capacity of the sucker rods. GL and HJP will be limited due to the injection pressure available of gas and water respectively. For the ESP systems power transmission is limited by the capacity of the motor drive, seals and pumps shafts.
Down-hole temperature – The two most vulnerable systems to downhole temperature are PCP and ESP. In the case of PCP, temperature can affect elastomer swelling rate, as well as cause degradation of its mechanical properties. The temperature of the elastomer during the operation will depend on the downhole temperature, fluid refrigeration capacity and the heat-build up of the elastomer (hysteresis). In ESP systems, the temperature affects mainly dielectric properties of the motor and cable, as well as lubricating oil properties thereof. Equipment selection validating temperature resistance of materials and compatibility testing are recommended.
Solids handling – Sand production during first production stage of hydraulic fractured wells is typical. Internal components Stuck as well as subsuperficial pumps completely plugged are usual. At this stage PCP or HJP are often good alternatives which performance combines well with sand production until it is stable and not displaced from the completion.
Slim Hole Wells – Slim-hole wells have different restrictions for its completion. Casing inside diameter (ID) determines outside (OD) diameter of the tubing string, and this limits OD of the sucker rods and other internal components. A slim-hole well could restrict the OD of the ESP components as motor, seals and pumps, and its limit the diameter of the shafts. In summary, the power transmission from the motor to the pump is limited when PCP, SRP and ESP are used in slim hole completions. If a tubing-less completion is used, other mechanical challenges will appear in order to install and operate any ALS. Particularly in slim-hole wells, diverse operations in completion, intervention, wireline, and ALS operation themselves, become more difficult, increasing time, risks and costs.
Reference:
- OMAE2012-84124 – “Artificial Lift Management: recommendations for Unconventional Oilfields” (Fernando Flores Avila / Jaime Granados Caliz / PEMEX E&P – Clemente Marcelo Hirschfeldt / Oil Production Consulting)
- Revista Ciencia & Tecnología – Ecopetrol – “Artificial Lift Management: Recomendations and Sugestions of Best Practices” – Clemente Marcelo Hirschfeldt / Oil Production Consulting.
- SPE 124737 “Selection Criteria for Artificial Lift System Based on the Mechanical Limits: Case Study of Golfo San Jorge Basin, Argentina” – Clemente Marcelo Hirschfeldt, Rodrigo Ruiz; Oil Production Consulting
- www.artificiallift.net