When selecting steel type for pipes and connections it is important to consider the corrosive environment that the steel will be subjected to. There are several parameters in the well that affect the corrosion, like temperature, chloride ion concentration, partial pressure of CO2 and H2S, pH and presence or absence of Sulphur [Craig et al. 2011].
When selecting a material there are certain aspects that have to be taken into consideration [NORSOK M-001 2004]:
- Corrosivity;
- Design life;
- Availability;
- Failure possibility and the consequences related to failure;
- Resistance to brittle fracture;
API tubing steel grades are identified by letters and numbers which dictate various characteristics of the steel. For each grade, the number designates the minimum yield strength. Thus L-80 grade steel has a minimum yield strength of 80,000 psi. In other words, it can support a stress of 80,000 psi with an elongation of less than 0.5%. The letter in conjunction with the number designates parameters such as the maximum yield strength and the minimum ultimate strength which for L-80 pipe are 95,000 psi.
The following table shows the yield values for various API tubing grades:
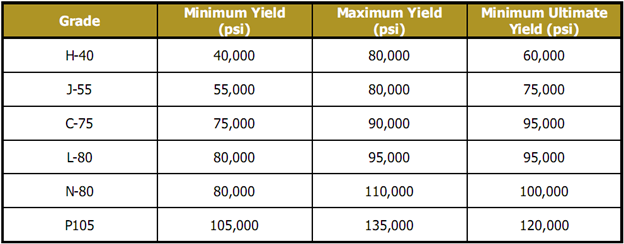
Continue reading →